Elevating Business with **ROC Welding** Techniques in Laser Cutting Machines
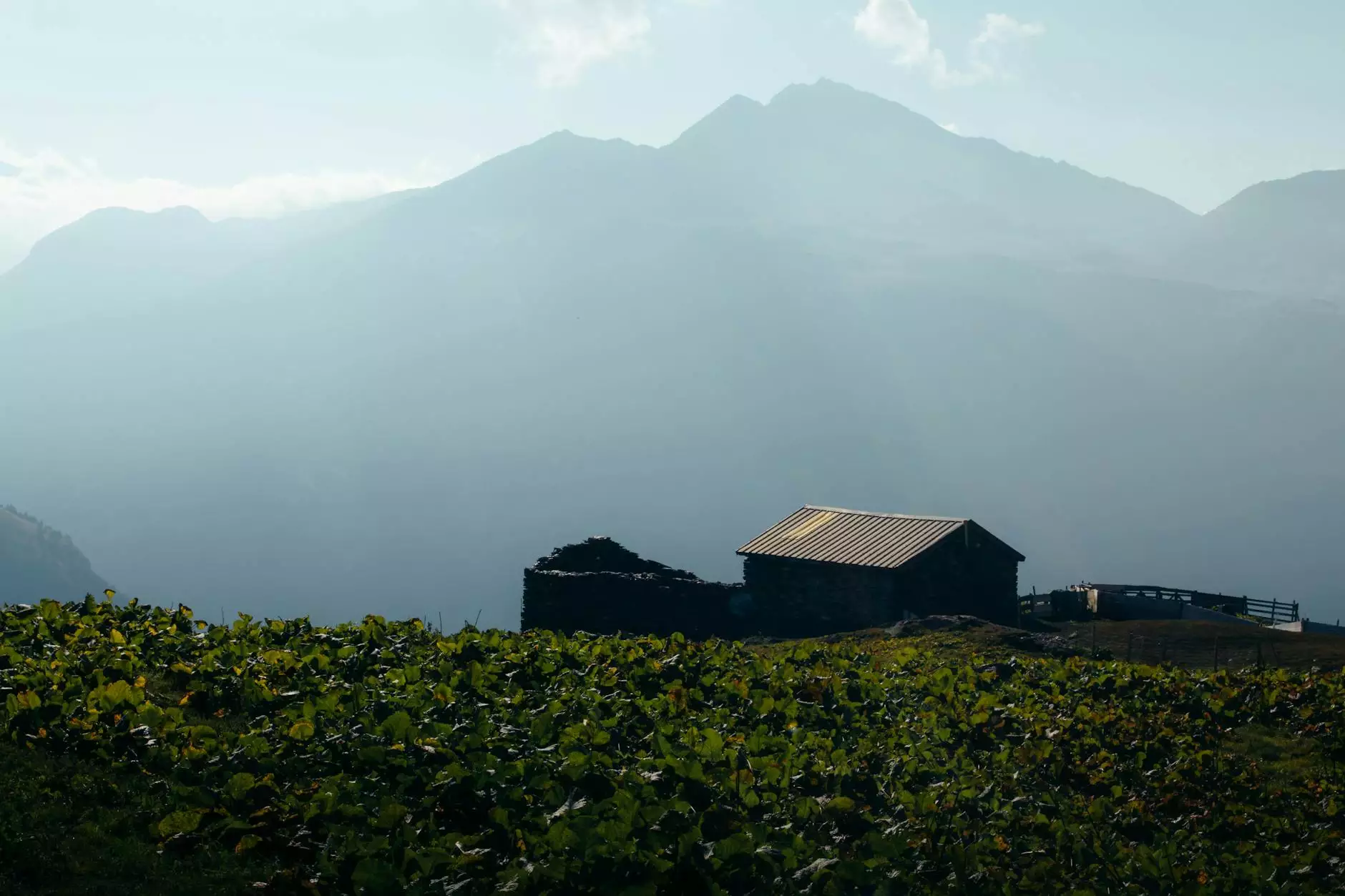
In the advanced world of manufacturing, precise cutting and welding are crucial for achieving high-quality products. At the forefront of this revolution is ROC welding, a technique that is seamlessly integrated into the operation of cutting-edge laser cutting machines. This article will explore how ROC welding not only enhances the functionality of laser cutting machines but also contributes significantly to the success of businesses in various sectors.
Understanding ROC Welding
ROC welding, or Robot Optimized Chain welding, epitomizes innovation in the welding industry. This method utilizes robotic systems to perform welding processes with unparalleled precision and speed. The advantages of ROC welding include:
- Increased Efficiency: Automation speeds up the welding process, minimizing downtime and maximizing output.
- Enhanced Precision: Robotic systems reduce human error, ensuring consistent quality in your welding projects.
- Versatile Applications: ROC welding is adaptable for various materials and thicknesses, offering businesses flexibility in production.
- Cost-Effectiveness: Although the initial investment may be high, the long-term savings and quality improvements justify the cost.
The Synergy Between ROC Welding and Laser Cutting Machines
When integrated with high-performance laser cutting machines, ROC welding amplifies productivity. Laser cutting machines are renowned for their ability to cut materials with precision. However, combining them with ROC welding can lead to remarkable enhancements in product development and manufacturing processes.
Key Advantages of Integration
Integrating ROC welding with laser cutting provides several key benefits:
- Streamlined Processes: The pairing reduces the number of workflows, allowing businesses to expedite production and minimize labor costs.
- Space Efficiency: By combining cutting and welding into one process, companies can utilize their workspace more effectively, leading to more organized production areas.
- Improved Product Quality: Precise laser cutting ensures that the materials fit together perfectly, reducing wastage and enhancing the strength of the final product.
- Data-Driven Insights: Advanced laser cutting machines and ROC welding robots can collect data that can be analyzed to optimize further production and quality control processes.
Industry Applications of ROC Welding in Laser Cutting
ROC welding is transforming several industries through its integration with laser cutting technology. Here's how various sectors are benefiting:
1. Automotive Industry
In automotive manufacturing, precision is paramount. The combination of ROC welding and laser cutting enhances:
- Structural Integrity: Ensuring components are securely and accurately joined.
- Weight Reduction: Laser cutting allows for the creation of lightweight yet strong parts, improving vehicle performance.
- Mass Customization: Facilitation of unique configurations for different vehicle models without significant retooling costs.
2. Aerospace Sector
The aerospace industry demands the highest standards for safety and reliability. ROC welding, when used with laser cutting, allows manufacturers to achieve:
- High Tolerance Levels: Producing components that meet stringent aviation standards.
- Complex Geometries: Laser cutting machine capabilities enable intricate designs that meet functional needs without compromising structural integrity.
- Operational Efficiency: Faster production rates can significantly reduce lead times for critical components.
3. Fabrication and Construction
In fabrication and construction, ROC welding combined with laser cutting simplifies complex assemblies, leading to:
- Faster Turnaround: Projects completed in a shorter time frame enhance competitiveness.
- Material Optimization: Reduced scrap and waste as cutting is done with extreme accuracy.
Choosing the Right Laser Cutting Machine for ROC Welding
Selecting the appropriate laser cutting machine that complements ROC welding capabilities is essential for businesses intending to optimize their manufacturing processes. Here are some key features to consider:
1. Power and Speed
The power of the laser directly influences the speed and efficiency of cutting operations. Machines with adjustable power settings can offer flexibility for different materials.
2. Type of Laser
Different types of lasers (fiber, CO2, etc.) have various applications and benefits. Understanding your specific needs will guide your choice effectively.
3. Automation Capabilities
Look for machines with automation options that can integrate seamlessly with robotics for ROC welding.
4. Software Integration
Advanced software allows for greater control and efficiency in both cutting and welding processes. Ensure compatibility with existing systems and ease of use for operators.
Future Trends in ROC Welding and Laser Cutting
The integration of ROC welding with laser cutting technology is not just a trend but a transformational shift within the manufacturing industry. Here are some anticipated future trends:
1. Advanced Robotics
As robotics technology advances, ROC welding will become even more precise and efficient. Enhanced AI capabilities will enable machines to learn and adapt during production processes, leading to even higher quality outcomes.
2. Eco-Friendly Practices
With increasing focus on sustainability, improved techniques in ROC welding and laser cutting will aim to minimize waste and energy consumption, aligning with global eco-friendly initiatives.
3. Customized Solutions
More personalized manufacturing will grow in popularity, with systems being able to cater to unique customer specifications seamlessly.
Conclusion
The fusion of ROC welding with advanced laser cutting machines is significantly reshaping the manufacturing landscape. By leveraging these technologies, businesses can finely tune their operations for enhanced efficiency, reduced costs, and superior product quality. As industries continue to evolve, adopting these innovative methods will position companies for long-term success in an increasingly competitive marketplace. Embracing the possibilities that ROC welding and laser cutting present can lead businesses not only to meet but to exceed their production goals and customer expectations.