Understanding the Importance of Air Compressor Inspection
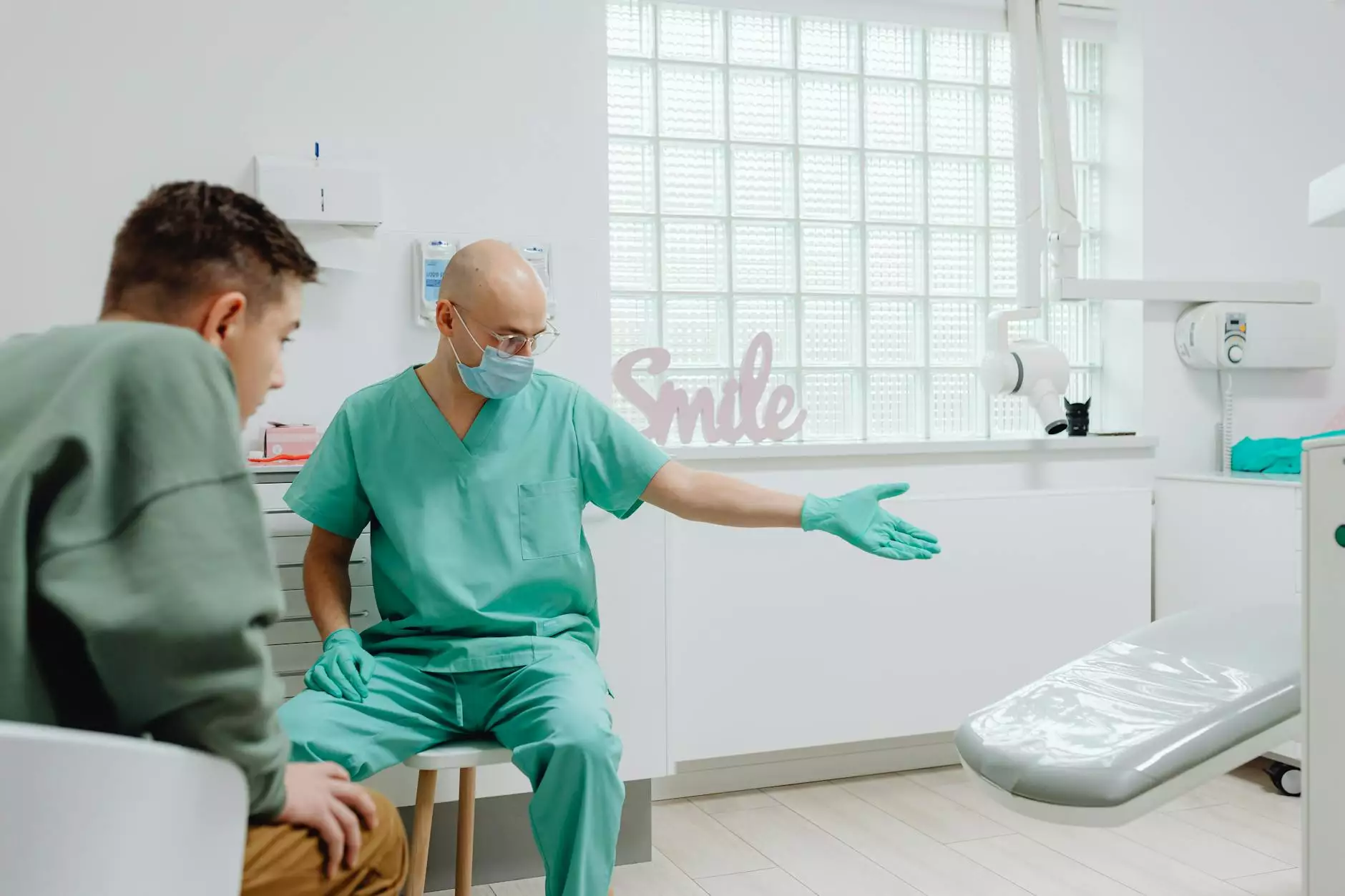
In the world of industrial and residential applications, air compressors have become essential tools. They serve a multitude of purposes, from powering pneumatic tools to providing air for various manufacturing processes. However, like any piece of machinery, they require regular inspections to maintain performance and safety. This article will delve into the significance of air compressor inspection, the steps involved, and how it can benefit businesses in the Home & Garden, Gardeners, and Pest Control sectors.
Why Air Compressor Inspection Matters
Regular inspection of air compressors is critical for several reasons:
- Safety: Faulty air compressors can pose safety risks, including explosions or injuries from malfunctioning equipment.
- Efficiency: An inspected and well-maintained compressor operates efficiently, reducing energy bills and improving overall productivity.
- Longevity: Regular inspections can identify potential issues before they become significant problems, thereby extending the lifespan of the equipment.
- Compliance: Many industries are required to adhere to safety regulations, and maintaining equipment through inspections helps meet these legal standards.
Key Components of Air Compressor Inspection
A thorough air compressor inspection involves assessing various components to ensure they are functioning optimally. Below are the essential components to consider during an inspection:
1. Valves
The valves in an air compressor play a critical role in ensuring that air flows correctly. During an inspection, it is essential to check:
- For any signs of wear or damage.
- If they are opening and closing properly.
- For leaks that could compromise performance.
2. The Pressure Switch
The pressure switch controls the on and off cycling of the air compressor. Inspect the pressure switch to ensure:
- It is calibrated correctly.
- It responds to pressure changes accurately.
- There are no visible signs of damage.
3. Air Filters
Clean air filters are vital for the efficient operation of an air compressor. During the inspection:
- Inspect air filters for dust and debris accumulation.
- Replace or clean filters as needed to maintain airflow.
4. Oil Levels
If the compressor is oil-lubricated, checking the oil levels is paramount. Ensure that:
- The oil is at the recommended level.
- The oil is clean and free of contaminants.
5. Hoses and Fittings
Hoses and fittings are subject to wear and can develop leaks over time. Inspect these components for:
- Brittleness or cracking.
- Loose connections or signs of leaks.
6. Pressure Relief Valve
To prevent excess pressure buildup, the pressure relief valve must function correctly. Inspect it for:
- Proper operation when tested.
- Signs of rust or damage.
Steps for Conducting an Air Compressor Inspection
Conducting an air compressor inspection may seem daunting, but breaking it down into manageable steps can simplify the process. Here is a systematic approach:
Step 1: Prepare the Compressor
Before starting the inspection, ensure the air compressor is turned off and has been disconnected from the power source. This step is critical for safety.
Step 2: Visual Inspection
Begin with a visual inspection of the unit. Check for:
- Signs of leaks or damage on the exterior.
- Corrosion around connections and fittings.
Step 3: Internal Checks
If applicable, access the interior components of the compressor. Look for:
- Signs of oil leaks inside the tank.
- Debris accumulation that could affect operation.
Step 4: Functional Testing
Power on the compressor and conduct a functional test. Observe for:
- Unusual noises or vibrations.
- Check the gauges to ensure they are functioning correctly.
Step 5: Document Findings
It is essential to maintain a record of all inspections conducted, including any issues found and the actions taken. This documentation can be invaluable for future reference and compliance checks.
Best Practices for Air Compressor Maintenance
Along with regular inspections, adhering to best practices can help maintain the efficiency and safety of air compressors in business settings:
- Schedule Routine Inspections: Routine inspections should be scheduled at least once every six months, or more frequently if the compressor is used heavily.
- Keep Records: Maintain thorough records of all inspections and maintenance activities.
- Invest in Quality Equipment: When purchasing new compressors, invest in high-quality models known for reliability.
- Train Employees: Provide training for employees who operate air compressors to understand their maintenance needs.
Environmental Considerations
In today's business environment, it is increasingly important to consider the environmental impact of equipment. Proper air compressor inspection can lead to better energy efficiency which, in turn, lowers energy consumption and reduces carbon footprints. Furthermore, maintaining compressors in optimal condition limits the risk of leaks that could result in harmful emissions.
Conclusion
In conclusion, regular air compressor inspections are paramount for ensuring safety, efficiency, and compliance with industry standards. By understanding the components involved, following systematic inspection procedures, and adhering to best practices, businesses—especially those within the Home & Garden, Gardeners, and Pest Control sectors—can maintain their equipment in excellent condition. Prioritizing these inspections not only protects employees and customers but also enhances the overall performance of operations. Make it a point to assess your air compressor regularly and invest in its upkeep—it’s a small action with a significant impact.